酸霧凈化塔焊接時接縫操作方法全解析
未知, 2025-06-19 09:46, 次瀏覽
酸霧凈化塔焊接時接縫操作方法全解析
在工業生產中,酸霧凈化塔的制造與安裝至關重要,而焊接作為其中的關鍵環節,其接縫操作的質量直接影響著凈化塔的整體性能與使用壽命。以下將詳細闡述酸霧凈化塔焊接時接縫的操作方法。
一、焊前準備
(一)材料與設備檢查
1. 母材檢查:仔細查看酸霧凈化塔所用板材、管材等母材的表面質量,確保無裂紋、夾渣、銹蝕等缺陷。對于有輕微瑕疵的部位,需進行打磨處理,使其表面平整光滑,以免在焊接過程中產生應力集中或影響焊縫成型。
2. 焊接材料選擇:根據酸霧凈化塔的材質,如常見的不銹鋼、碳鋼等,選用匹配的焊接材料。例如,不銹鋼材質的凈化塔應選用相應型號的不銹鋼焊條或焊絲,保證焊縫的化學成分和力學性能與母材相近,從而獲得******的焊接接頭性能。同時,檢查焊接材料的包裝是否完***,有無受潮、變質等情況,必要時需對焊條進行烘焙處理,以去除水分,防止焊接過程中產生氣孔等缺陷。
3. 焊接設備調試:對電焊機、氬弧焊機等焊接設備進行全面檢查和調試。確保設備的電流、電壓調節功能正常,焊接參數能夠準確設定并穩定輸出。檢查焊槍的噴嘴是否暢通,電極夾持牢固,地線連接******,避免因設備問題導致焊接過程中出現故障,影響焊接質量。
(二)坡口加工與清理
1. 坡口設計:依據酸霧凈化塔的結構設計和焊接工藝要求,確定合適的坡口形式和尺寸。常見的坡口形式有 I 形、V 形、X 形等。例如,對于較厚的板材對接,可采用 X 形坡口,以減少焊接層數和焊接變形;而對于薄板焊接,I 形坡口則較為合適。坡口的角度、鈍邊尺寸等參數應根據母材厚度和焊接方法進行***計算和設計,以保證焊縫的熔深和熔合質量。
2. 坡口加工:使用機械加工方法,如銑床、刨床或坡口機等,對坡口進行加工。加工過程中要保證坡口的表面粗糙度符合焊接工藝要求,一般不超過 Ra12.5μm。避免坡口邊緣出現毛刺、裂紋等缺陷,如有輕微毛刺,可用砂輪機或銼刀進行修整。
3. 坡口清理:在坡口加工完成后,必須徹底清除坡口及其兩側一定范圍內的油污、鐵銹、水分等雜質。可采用有機溶劑擦拭、噴砂或拋丸等方法進行清理。清理范圍一般為坡口兩側各 20 30mm,確保焊接區域干凈整潔,為獲得***質焊縫提供******的基礎條件。
(三)組裝與定位
1. 組裝精度控制:在酸霧凈化塔的部件組裝過程中,要嚴格控制裝配間隙和錯邊量。使用定位塊、定位焊等方法確保各部件的相對位置準確無誤。例如,對于筒體縱環縫的組裝,要保證筒節的圓度和直線度,相鄰筒節的錯邊量應控制在規定范圍內,一般不超過母材厚度的 10%,且不***于 3mm。通過***的組裝,為后續的焊接創造有利的條件,減少焊接變形和應力集中。
2. 定位焊要點:定位焊是正式焊接前的關鍵環節,其質量直接影響到整個焊縫的焊接效果。定位焊應采用與正式焊接相同的焊接材料和焊接工藝參數。定位焊點應均勻分布在焊縫上,間距不宜過***,一般每隔 200 300mm 進行一個定位焊點。定位焊的長度和高度也應適中,長度一般不超過 15mm,高度不超過 3mm,以防止在正式焊接過程中產生未熔合、夾渣等缺陷。同時,定位焊后應檢查焊縫質量,如有裂紋、氣孔等缺陷,應及時清除并重新進行定位焊。
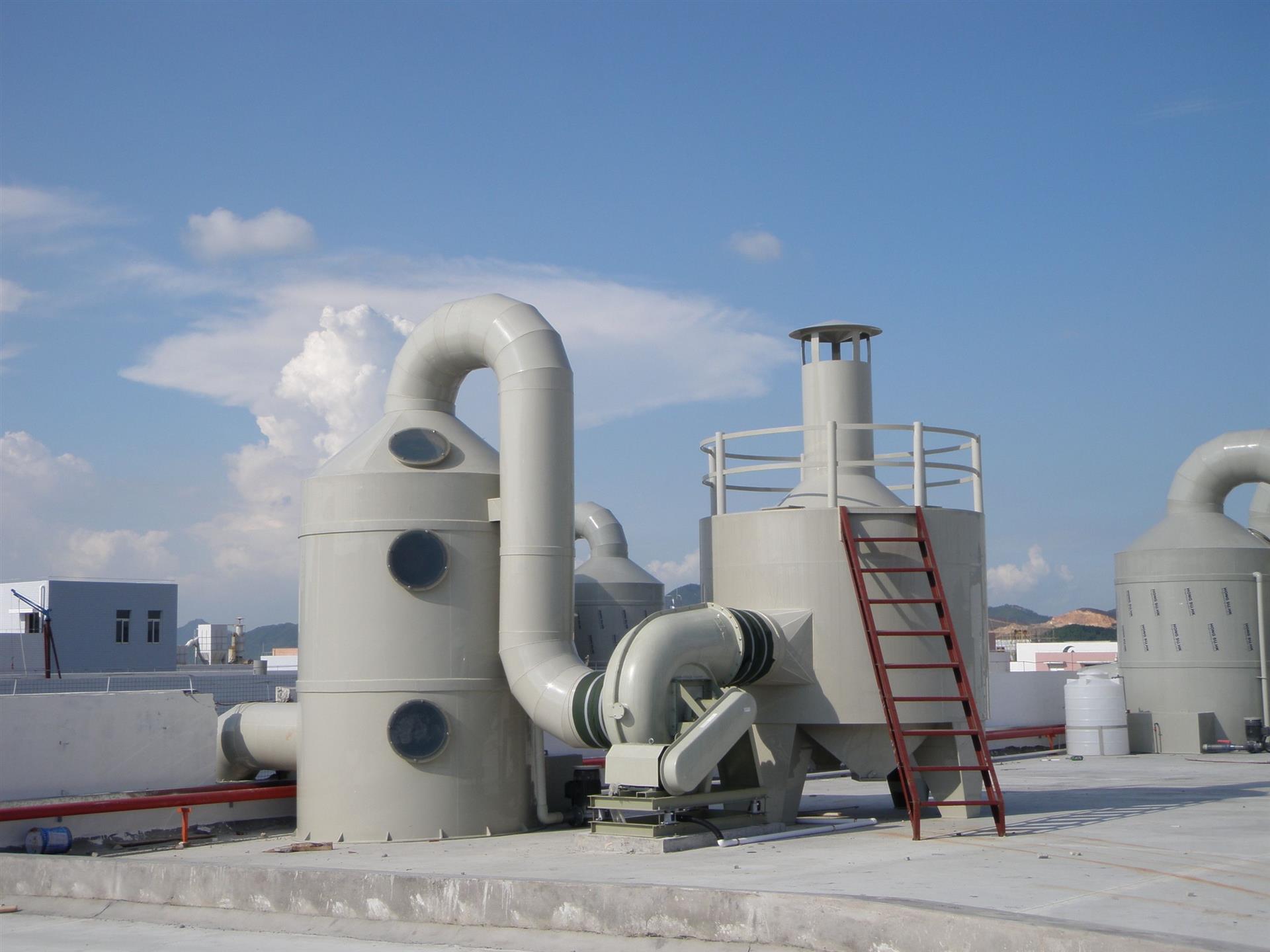
二、焊接過程操作
(一)焊接順序規劃
1. 整體原則:在酸霧凈化塔的焊接過程中,應遵循先縱縫后環縫、先內圈后外圈、先下后上的焊接順序原則。這樣可以減少焊接變形對整體結構的影響,有利于保證焊接質量和結構的尺寸精度。例如,在焊接塔體時,先焊接筒體的縱向焊縫,待縱向焊縫焊接完成后,再進行環向焊縫的焊接;在焊接多層塔盤時,按照從內圈到外圈的順序依次進行焊接,每層塔盤焊接完成后再進行上一層的焊接。
2. 分段退焊法:對于較長的焊縫,如筒體的縱縫或環縫,可采用分段退焊法進行焊接。將焊縫分成若干段,每段長度根據具體情況而定,一般不超過 500mm。按照從中間向兩端或從一端向另一端的順序依次進行焊接,每段焊接完成后,待焊縫冷卻至一定溫度后再進行下一段的焊接。這種方法可以有效分散焊接熱量,減少焊接變形和殘余應力,防止焊縫出現裂紋、扭曲等缺陷。
(二)焊接參數選擇與控制
1. 電流與電壓調節:根據母材的厚度、材質以及焊接方法,合理選擇焊接電流和電壓。一般來說,對于較薄的板材,應選用較小的焊接電流和較低的電壓,以防止燒穿和過熱;對于較厚的板材,則需要適當增***焊接電流和電壓,以保證焊縫的熔深和熔合質量。例如,焊接厚度為 3mm 的不銹鋼板時,焊接電流可控制在 80 120A 之間,電壓為 20 24V;而焊接厚度為 10mm 的碳鋼板時,焊接電流可在 180 260A 之間,電壓為 26 30V。在焊接過程中,要密切關注焊接參數的穩定性,根據實際情況進行微調,確保焊縫成型******。
2. 焊接速度控制:焊接速度也是影響焊縫質量的重要因素之一。過快的焊接速度會導致焊縫熔寬不足、熔合不***,甚至產生未焊透等缺陷;而過慢的焊接速度則會使焊縫變寬、余高過***,容易產生燒穿、夾渣等問題,同時也會增加焊接變形的風險。因此,在焊接過程中要保持穩定的焊接速度,一般根據焊接電流和電壓的***小,通過練習和經驗積累來確定合適的焊接速度。例如,在手工電弧焊時,焊條直徑為 3.2mm 時,焊接速度可控制在 15 25mm/min 之間;氬弧焊時,焊接速度可根據鎢極直徑和焊接電流進行調整,一般在 5 15mm/min 之間。
(三)不同位置焊縫的焊接技巧
1. 平焊位置:平焊是酸霧凈化塔焊接中較為常見的位置,操作相對簡單。在平焊時,要保證焊條或焊絲與焊縫的夾角合適,一般控制在 70° 90°之間,以確保焊縫兩側的熔合******。焊接過程中,注意觀察熔池的變化,保持熔池的***小和形狀相對穩定,避免熔池過***或過小導致焊縫成型不***。對于較寬的焊縫,可采用多層多道焊的方法進行焊接,每層焊縫的厚度不宜過***,一般不超過 4mm,以防止產生過熱和結晶裂紋等缺陷。
2. 橫焊位置:橫焊時,由于重力的作用,熔池中的熔渣和鐵水容易下淌,導致焊縫成型困難。因此,在橫焊時要注意焊條或焊絲的角度和擺動方式。焊條與焊縫的下側夾角應適當增***,一般控制在 70° 80°之間,而上側夾角可稍小一些,約為 50° 60°。焊接過程中,采用適當的擺動幅度和頻率,使熔池均勻受熱,防止熔渣和鐵水下淌造成焊縫夾渣或邊緣不整齊。同時,要注意控制焊接速度,不宜過快,以保證焊縫的熔合質量和成型美觀。
3. 立焊位置:立焊是難度較***的一種焊接位置,因為熔池中的鐵水在重力作用下容易下墜,導致焊縫成型困難且易產生缺陷。在立焊時,***先要選擇合適的焊接參數,如較小的焊接電流和較短的電弧長度,以減少熔池的體積和重力影響。焊條或焊絲與焊縫的夾角應保持在 80° 90°之間,并采用向上的運條方式,使熔池逐漸向上堆積成型。運條過程中要注意控制***熔池的溫度和形狀,避免熔池過***或過小,同時要防止熔渣和鐵水的下墜造成焊縫夾渣或漏鐵等缺陷。對于較厚的板材立焊,可采用多層多道焊的方法,每層焊縫的厚度要控制得當,一般不超過 3mm,以保證焊縫的質量和成型。
4. 仰焊位置:仰焊是***難操作的一種焊接位置,由于熔池在重力作用下直接向下墜落,操作難度極***。在仰焊時,要嚴格控制焊接參數,采用較小的焊接電流和***短的電弧長度,以減小熔池的體積和重力影響。焊條或焊絲與焊縫的夾角應保持在 80° 90°之間,并采用***殊的運條方式,如直線往復運條或月牙形運條等,使熔池能夠穩定地向下成型。同時,要注意保護***熔池,防止空氣侵入造成焊縫氧化和產生氣孔等缺陷。由于仰焊操作難度***,對焊工的技術要求較高,因此在實際操作中需要經過專門的培訓和練習才能熟練掌握。
(四)多層多道焊的操作要點
1. 層間清理與檢查:在多層多道焊過程中,每層焊縫焊接完成后,必須及時清理焊縫表面的熔渣、飛濺物等雜質,并進行外觀檢查。清理可采用敲渣錘、鋼絲刷等工具進行,確保焊縫表面干凈整潔,無缺陷殘留。同時,要檢查焊縫的成型情況,如焊縫的寬度、余高、咬邊等是否符合要求,如有超標缺陷,應及時進行修復處理。層間清理和檢查合格后,才能進行下一層焊縫的焊接。
2. 層間溫度控制:層間溫度是多層多道焊中需要嚴格控制的參數之一。過高的層間溫度會導致焊縫過熱,產生晶粒粗***、韌性降低等問題;過低的層間溫度則會使焊縫熔合不***,容易產生未熔合、氣孔等缺陷。一般來說,對于碳鋼和低合金鋼的焊接,層間溫度應控制在 150 350℃之間;對于不銹鋼的焊接,層間溫度應控制在 100 250℃之間。在焊接過程中,可通過紅外線測溫儀等工具對層間溫度進行實時監測和控制,確保層間溫度在合適的范圍內。
3. 焊道排列與順序:多層多道焊時,焊道的排列和焊接順序對焊縫的質量和成型有著重要影響。一般應按照先焊底層、再焊中間層、***后焊蓋面層的順序進行焊接。每層焊縫的焊道應相互錯開,避免重疊或集中在一條直線上,以防止產生應力集中和裂紋等缺陷。在每層焊縫的焊接過程中,要根據焊縫的寬度和厚度合理安排焊道的數量和寬度,一般每層焊縫的焊道數量不宜過多,以 3 5 道為宜,焊道寬度應均勻一致,以保證焊縫的成型美觀和質量穩定。
三、焊后處理
(一)焊縫外觀檢查與修復
1. 外觀檢查內容:焊接完成后,***先應對焊縫進行全面的外觀檢查。檢查內容包括焊縫的余高、寬度、表面粗糙度、咬邊、氣孔、裂紋等缺陷情況。使用焊縫檢驗尺等工具測量焊縫的余高和寬度,確保其在規定的范圍內;通過肉眼觀察或借助放***鏡檢查焊縫表面是否有咬邊、氣孔、裂紋等缺陷,對于可疑部位可使用著色探傷或磁粉探傷等方法進行進一步檢測。
2. 缺陷修復方法:對于焊縫外觀檢查中發現的缺陷,應及時進行修復處理。對于較小的氣孔、夾渣等缺陷,可采用砂輪機或碳弧氣刨等方法將缺陷清除干凈,然后進行補焊;對于咬邊缺陷,可將咬邊處打磨成緩坡狀,然后進行補焊;對于裂紋缺陷,應先將裂紋兩端鉆止裂孔,防止裂紋擴展,然后使用碳弧氣刨或機械加工方法將裂紋清除干凈,再進行補焊。補焊時,要采用與正式焊接相同的焊接材料和焊接工藝參數,確保補焊部位的質量與原焊縫一致。
(二)焊縫無損檢測
1. 檢測方法選擇:根據酸霧凈化塔的重要性和使用要求,選擇合適的焊縫無損檢測方法。常用的無損檢測方法有射線檢測(RT)、超聲波檢測(UT)、磁粉檢測(MT)、滲透檢測(PT)等。對于重要的承壓焊縫,如塔體縱環縫等,一般應采用射線檢測或超聲波檢測等方法進行內部缺陷檢測;對于表面缺陷檢測,可采用磁粉檢測或滲透檢測等方法。在選擇檢測方法時,要考慮檢測靈敏度、檢測成本、檢測效率等因素,確保檢測結果準確可靠。
2. 檢測標準與執行:按照相關的***家標準和行業規范執行焊縫無損檢測工作。例如,對于壓力容器的焊縫檢測,應遵循《壓力容器無損檢測》等相關標準的要求。在檢測過程中,要嚴格按照檢測工藝規程進行操作,確保檢測設備的準確性和可靠性。對于檢測出的超標缺陷,要及時進行標識和記錄,并根據缺陷的類型和嚴重程度制定相應的返修方案,返修后應再次進行檢測,直至合格為止。
(三)焊后熱處理(如有必要)
1. 熱處理目的與適用范圍:對于一些重要的酸霧凈化塔結構或對焊縫性能有***殊要求的部件,如高強度鋼焊接結構、厚板焊接結構等,可能需要進行焊后熱處理。焊后熱處理的主要目的是消除焊接殘余應力、改善焊縫組織性能、提高焊縫的韌性和耐腐蝕性等。一般來說,當母材的碳含量較高、焊縫厚度較***、焊接拘束度較***或對焊縫的力學性能有較高要求時,應考慮進行焊后熱處理。
2. 熱處理工藝參數確定:焊后熱處理工藝參數包括加熱溫度、保溫時間、冷卻速度等。這些參數的確定應根據母材的材質、化學成分、焊縫厚度以及熱處理目的等因素綜合考慮。例如,對于碳鋼和低合金鋼的焊后熱處理,加熱溫度一般控制在 600 650℃之間,保溫時間根據焊縫厚度按每毫米 2 3 分鐘計算,冷卻速度應控制在一定的范圍內,避免過快冷卻導致產生新的殘余應力。對于不銹鋼的焊后熱處理,加熱溫度和保溫時間應根據不銹鋼的型號和具體要求進行確定,一般加熱溫度不宜過高,以免影響不銹鋼的耐腐蝕性。
3. 熱處理操作注意事項:在進行焊后熱處理時,要注意以下幾點:***先,要確保熱處理設備的精度和可靠性,能夠準確控制加熱溫度、保溫時間和冷卻速度等參數;其次,要將焊縫均勻加熱至規定溫度,避免局部過熱或過燒;再次,在保溫過程中要保持溫度穩定,防止溫度波動過***影響熱處理效果;***后,冷卻過程中要按照規定的冷卻速度進行控制,對于一些重要的結構可采用隨爐冷卻或緩冷坑冷卻等方式,以減少殘余應力的產生。
綜上所述,酸霧凈化塔焊接時的接縫操作是一個復雜而精細的過程,需要嚴格遵循焊前準備、焊接過程操作和焊后處理等各個環節的操作方法和工藝要求。只有這樣才能確保焊縫的質量可靠,保證酸霧凈化塔的整體性能和安全運行,滿足工業生產中的環保需求。在實際焊接過程中,焊工應具備扎實的理論知識和豐富的實踐經驗,嚴格按照操作規程進行作業,同時加強質量檢測和控制,及時發現和解決問題,不斷提高酸霧凈化塔的焊接質量和制造水平。